
Understanding the role and upkeep of bearings can significantly enhance the efficiency and lifespan of machinery and equipment. Bearings are critical components that minimize friction between moving parts, aiding in smoother operations and reducing wear. Ensuring they are maintained properly is therefore paramount.
Understanding Bearings and Their Importance
Bearings are mechanical assemblies that constrain relative motion while reducing friction between two or more parts. The most common types include ball bearings, roller bearings, and needle bearings. Each type serves specific functions depending on the load and movement required.
Ball Bearings
These are versatile bearings primarily used for low-load applications. They feature spherical rolling elements that allow for smooth rotations at high speeds with minimal friction.
Roller Bearings
Aimed at supporting heavier loads than ball bearings, roller bearings use cylindrical rolling elements. They're often employed in industrial machinery where both radial and axial loads need handling.
Needle Bearings
Characterized by their slender rollers, needle bearings have a high length-to-diameter ratio. These are particularly useful in scenarios requiring compact designs with higher load-carrying capacities.
Regular maintenance keeps these bearings performing optimally, thus preventing downtime, costly repairs, and inefficient machine operation.
Common Causes of Bearing Failure
Bearing failure can stem from various sources, but some of the most prevalent causes include:
Contamination: Dirt, dust, and other contaminants can infiltrate bearing surfaces, causing abrasion and premature failure.
Lubrication Issues: Insufficient or inappropriate lubrication leads to excess friction and heat buildup, resulting in bearing wear and tear.
Misalignment: When bearings are not correctly aligned during installation, uneven stress distribution occurs, accelerating deterioration.
Overloading: Exceeding the recommended load capacity puts unnecessary strain on bearings, leading to faster degradation.
Wear and Tear: Normal usage eventually results in material fatigue. Regular inspections help identify and replace worn-out bearings before failure affects system performance.
Tools and Materials Needed for Bearing Maintenance
Effective bearing maintenance requires specific tools and materials, including:
- Cleaning supplies: Solvents, brushes, and cleaning cloths.
- Lubricants and grease: Choose based on the manufacturer's recommendations for your specific bearing type and application.
- Specialized bearing tools: Pullers and presses for removal and installation, as well as micrometers and calipers for precise measurements.
- Safety gear: Protective gloves, safety glasses, and appropriate workwear to ensure personal safety.
Step-by-Step Bearing Inspection
An effective inspection process begins with an initial visual check followed by detailed procedures:
Initial Visual Inspection
Begin by examining the bearing for obvious signs of damage or contamination. Check the operating environment to ensure it's conducive to proper bearing function.
Detailed Inspection Procedures
Conduct rotational tests to assess smoothness. Measure clearance to detect excessive play using micrometers or calipers. Perform noise and vibration analysis with specialized equipment to pinpoint potential issues.
Cleaning and Lubrication Techniques
Cleaning Process
Start by disassembling the bearing carefully. Use appropriate methods and solutions for thorough cleaning. Ensure all components are completely dry before reassembly.
Lubrication Process
Select suitable lubricants, be it oil or grease, tailored to your bearing's requirements. Apply evenly and avoid over-lubrication. Maintain a regular re-lubrication schedule according to operational demands.
Correct Installation Practices
Proper installation ensures longevity and efficient functioning of bearings. Preparation involves inspecting the bearing and housing for cleanliness and readiness. Two primary mounting techniques include cold mounting, which uses mechanical tools, and hot mounting, employing heat to expand the bearings for easy fitting. Always confirm alignment post-installation and perform checks to verify correct assembly.
Monitoring and Predictive Maintenance
Establish a routine inspection schedule to catch potential issues early. Leverage technology like vibration analysis tools and temperature monitoring systems for predictive insights. Recording and analyzing data over time helps refine maintenance practices and extend bearing life.
Troubleshooting Common Bearing Problems
Identify symptoms such as unusual noises, excessive vibrations, or temperature spikes promptly. Immediate corrective actions may involve re-lubrication, realignment, or replacing damaged bearings. For long-term solutions, review maintenance routines and consider upgrades if recurring issues persist.
Advanced Tips for Bearing Longevity
Control environmental factors like dust and moisture, and regulate temperatures to mitigate adverse conditions affecting bearings. Upgrading to higher-quality bearings and integrating advanced lubrication systems can substantially increase durability.
Resources and Further Reading
Dive deeper into bearing maintenance through recommended books and guides. Engage with online forums and communities for practical insights. Familiarize yourself with industry standards and guidelines to stay updated.
FAQs on Bearing Maintenance
Address commonly asked questions and provide detailed answers to assist new users. Share quick tips and expert advice tailored to specific scenarios encountered during bearing maintenance.
Explore Youyi for top-grade auto parts, ensuring quality and reliability for all your machinery needs. Visit our website to learn more about our offerings: Youyi - Quality Auto Parts Focusing on Bearings.
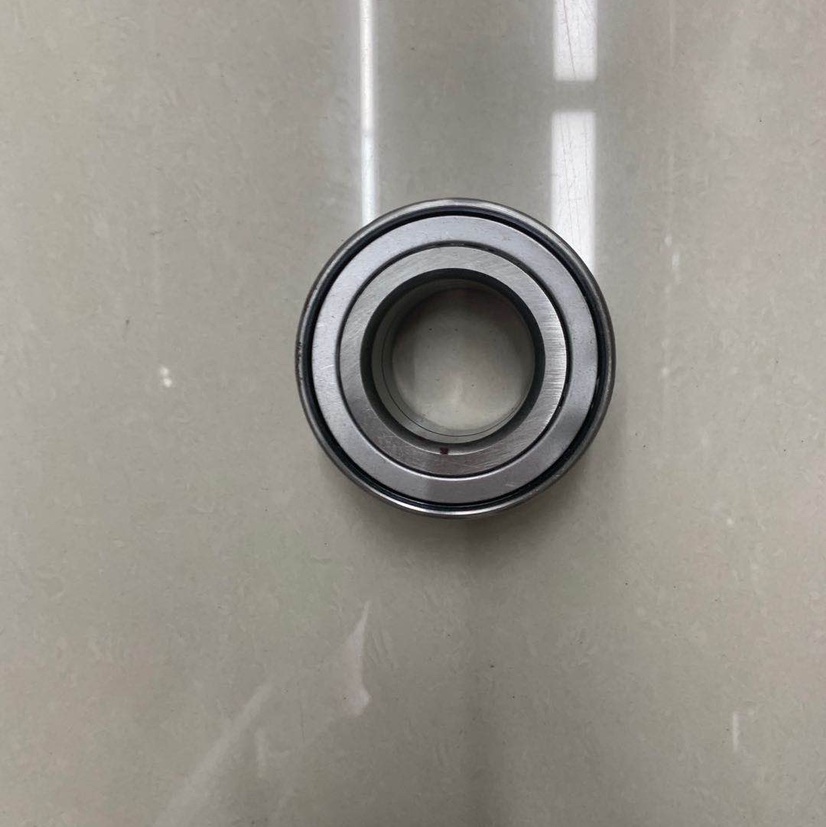