
The importance of proper bearing installation in any machinery cannot be overstated. Bearings are fundamental components that directly impact the performance, efficiency, and lifespan of equipment. Improper installation can compromise machine integrity, leading to increased wear, operational disruptions, or even catastrophic failure. This blog aims to elucidate the essential do's and don'ts for optimal bearing installation, ensuring your machinery functions at its best.
Do’s for Bearing Installation
Use the Right Tools
A successful bearing installation begins with using the right tools. Employing appropriate bearing pullers and presses ensures that bearings are installed and removed without causing damage. Precision measurement instruments, such as calipers and micrometers, are also crucial to confirm dimensions align perfectly with manufacturer specifications.
Cleanliness is Crucial
Dirt and contaminants can wreak havoc on bearings. Thus, thorough cleaning of both the bearing and housing before installation is imperative. Utilizing lint-free cloths and suitable cleaning agents guarantees that all surfaces remain uncontaminated. Any small particle left behind can lead to premature wear and eventual bearing failure.
Correct Lubrication
Lubricant selection plays a pivotal role in bearing longevity. Using the correct type and quantity shields the bearing from frictional forces and reduces heat generation. Adhering to proper lubrication methods as outlined by the lubricant manufacturer helps maintain optimal operating conditions. Over or under-lubricating can lead to adverse effects.
Follow Manufacturer Guidelines
Manufacturers provide specific guidelines tailored to the unique attributes of their bearings. Strictly following installation instructions, including recommended torque settings and techniques, assures the bearing performs as designed. Ignoring these guidelines risks improper installation, which may lead to premature failures.
Don’ts for Bearing Installation
Avoid Contaminants
Keeping dirt, dust, and moisture far away from bearings during handling and installation prevents potential failures. It is advisable not to open the bearings until you are ready for installation to minimize exposure to environmental contaminants.
Never Use Improper Force
Bearing installations should never involve hammering or striking, as this could cause irreversible damage to the bearing structure. Instead, use controlled force distribution methods like hydraulic presses to ensure an even fit without excess pressure that might deform integral parts.
Don’t Ignore Alignment
Proper alignment during installation is critical. Misalignment can introduce uneven loads on the bearing raceways, escalating wear and reducing lifespan. Careful attention to detailed alignment checks will help avoid early fatigue and breakdowns.
Steer Clear of Overheating
Applying improper heating techniques for thermal expansion affects bearing properties. Avoid direct flame or uneven heating, opting instead for controlled solutions like induction heaters or hot oil baths. These methods allow uniform temperature increase, facilitating easier fitting while preserving material integrity.
Troubleshooting Common Issues
Identifying Symptoms of Poor Installation
Common symptoms indicating poor bearing installation include unusual noise, vibrations, and excessive heat production. Visual inspections revealing discoloration, scoring, or uneven wear patterns further indicate incorrect installation practices.
Correcting Installation Errors
If misalignment or contamination issues arise, corrective measures include realigning with calibrated tools, re-cleaning the components, and re-lubricating according to precise amounts specified. Identifying signs early allows rectification before extensive damage ensues.
Maintenance Tips Post-Installation
Regular Inspection and Monitoring
Ongoing vigilance through scheduled maintenance checks ensures bearing integrity over time. Condition monitoring tools, including vibration analyzers and thermographic cameras, aid in detecting anomalies promptly.
Re-lubrication Practices
Bearings often require periodic re-lubrication based on load conditions and operating environment. Establishing intervals helps maintain consistent performance; indicators such as higher operational temperatures signal when re-lubrication is necessary.
Real-World Applications and Case Studies
Success Stories
Certain companies have achieved remarkable improvements in machinery reliability through stringent adherence to proper bearing installation protocols. Optimized installation has extended service intervals and minimized unexpected downtimes.
Lessons from Failures
Learning from past errors provides invaluable insights. Cases where bearings failed due to haste, neglect, or absence of adequate preparation illustrate the grave impacts improper practices can foster. Detailed analyses often reveal laxness during initial stages as primary culprits.
Resources for Further Learning
Manufacturer Resources
Tap into a wealth of knowledge provided by manufacturers through guides and manuals specifically curated for diverse bearing types. Online training modules and step-by-step video tutorials offer practical learning experiences.
Professional Courses and Certifications
Engaging in specialized workshops and obtaining certifications elevate expertise and acquaint users with current industry standards. Continuous education keeps professionals updated on evolving best practices related to bearing maintenance and installation.
Embodying these core principles in your daily operations not only enhances bearing life but boosts overall machinery effectiveness, promising seamless functionality and minimizing costly interruptions. If you're looking to source quality bearings, consider exploring options at Youyi Good Auto Parts Firm, known for reliable auto parts engineered to uphold the highest standards.
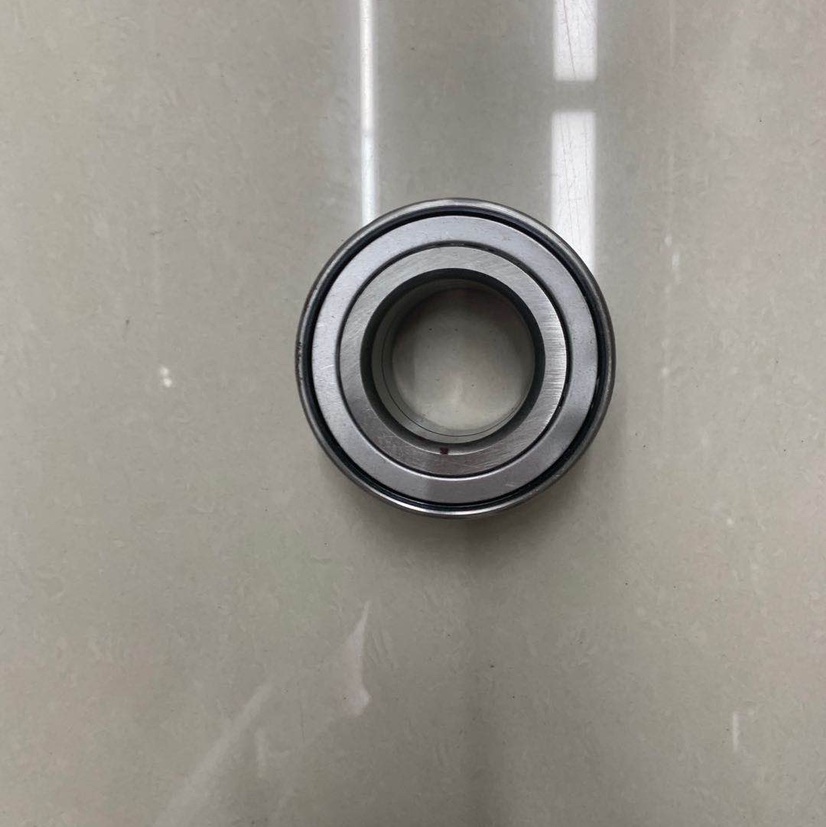